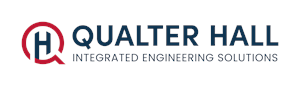
Qualter, Hall & Company Limited
Stand B07
Qualter Hall provides comprehensive MEICA solutions across the project lifecycle, from concept to operation and beyond.
Our portfolio boasts iconic bridges of diverse sizes and types, including the Great Yarmouth Third River Crossing, the Sean O’Casey Bridge over Dublin’s River Liffey, Hull's Scale Lane swing bridge, the Montgomery Bridge in Canary Wharf, Breydon Bridge on the River Yare and many more.
With a skilled workforce and advanced UK-based manufacturing, we deliver innovative and reliable solutions for complex engineering challenges.
Documents
-
Qualter Hall & Company Ltd: Bridges BrochureExperts in bridge design and engineering New Supply, Reconstruction, Refurbishment, and Upgrades for Moving and Static Bridges. Qualter Hall has been involved in the design, manufacture, fabrication, installation, commissioning and ongoing maintenance of a multitude of bridges of varying types and sizes. Our team can provide a full ‘cradle to grave’ turnkey service or supply elements such as the mechanical and electrical operating package for your structure.
-
Qualter Hall & Company Ltd: BrochureQualter Hall & Company Ltd delivers Mechanical, Electrical, Instrumentation, Control and Automation (MEICA) services to a multitude of industry sectors.
Brands
-
Hugh Smith Machines
Products
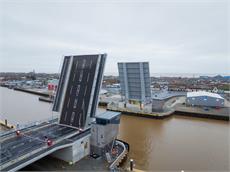
Great Yarmouth Third River Crossing ('Herring Bridge')
MEICA system fabricated by Qualter Hall.
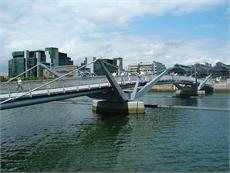
The Sean O'Casey Bridge, Double Leaf Pedestrian Swing Bridge, River Liffey, Dublin
The Sean O'Casey Bridge is a double leaf pedestrian swing bridge over the River Liffey near Custom House Quay in Dublin. The bridge was part of a large scale urban renewal scheme under the Dublin Docklands Development Authority, to link both the north and south quays and rejuvenate both.
Appointed by main civil contractor John Mowlem Construction Ltd, Qualter Hall delivered the complete design of the mechanical, electrical and hydraulic operating and control systems for the bridge. Also for the detail and incorporation of the client’s initial structural design into fabrication drawings.
Two bridge leafs each measuring 44m nose to tail and 4.5m wide, provide a river crossing of 88m bank to bank. These swing open to allow boats to pass along the river. Each leaf, weighing 180 tonnes, rotates on a centre pivot driven through 90 degrees by twin hydraulic cylinders, with interlocked hydraulic nose and tail bolts. Hydraulic power units and electrical controls are located below the deck adjacent to the centre pivots.
Each bridge leaf is supported centrally on a fabricated cradle having four arms, which are located at either side of the walkway area. The bridge decks are supported at both extremities with a cable rod system, which is connected to the tips of the cradle arms. The deck is constructed from aluminium hollow section profiles and both sides are fitted with stainless steel protective handrail and balustrade infill panels.
Each bridge leaf pivots horizontally on a slew bearing that is secured to the central fabrication, which in turn is anchored to the top of the concrete support plinth in the river.
The bridge is operated locally by radio pendant, with pedestrian gates being closed prior to operation.
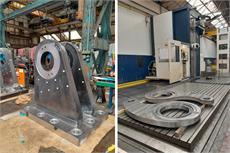
Waterford Bridge, Ireland (work in progress)
Qualter Hall is supplying, installing and commissioning the MEICA equipment required to operate a new twin bascule bridge over the River Suir in Waterford, Ireland. The new sustainable transport bridge is being fabricated for Waterford City & County Council.
Components consist of mechanical parts, hydraulic systems and control equipment which will lift and lower the bascule leaves of the bridge.
The structure’s highly complex steel components have been fully manufactured in our UK-based facility, machined in our Soraluce machining centre, shotblasted, painted and assembled.
The whole system was designed by client consultants H&H and Roughan & O'Donovan, and detailed by our in-house design team.
Our engineers have been travelling to the Victor Buyck Steel Construction works in Belgium, to install our components onto the bridge before it is shipped to its final destination in Ireland for continued construction, assembly and commissioning by BAM UK & Ireland, supported by our team, which will also be training operatives to use the bridge's control system.
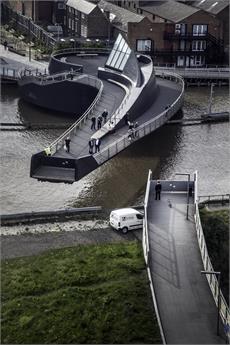
Scale Lane Bridge, River Hull
Scale Lane Bridge is a 57 metre span, 1000 tonne, pedestrian and cycle way swing bridge, connecting Scale Lane to Tower Street on opposite banks of the River Hull. The black steel bridge has a distinctive robust character and curving form, making it a memorable landmark that is unique to Hull and its industrial and maritime heritage.
The bridge was designed, fabricated, installed and commissioned by Qualter Hall, in sections in our facilities in Barnsley, transported to site, welded together on the river bank and then lifted into place across the river. Our team is also behind the mechanics, electrics and controls which enable the bridge to move. Our Site Services team commissioned the structure for Hull City Council, and trained the client’s operatives on-site.
The primary structure consists of a steel spine, cantilevering approximately 37m from a three-dimensional Vierendeel girder ring that is approximately 15m in diameter, with a circular structure which houses the glazed bistro/restaurant space.
The bridge’s sweeping form creates two generous pedestrian routes, one gently sloping and a shorter stepped walkway. The roof of the drum provides an upper viewing deck with a seamless steel balustrade, which gives the feeling of being on board a docked ocean liner.
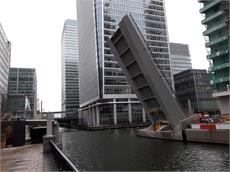
Montgomery Bridge, Canary Wharf, London
Qualter Hall were awarded a contract by Canary Wharf Contractors to deliver this single leaf Bascule Bridge installed within the Canary Wharf district of London.
The Montgomery Bridge has a 30m span, is 15m wide and weighs approximately 200 tonnes. It provides access for vehicular and pedestrian traffic from Montgomery Street to Wood Street, and lifts to allow the passage of marine craft.
Qualter Hall produced the MEICA design and fabricated the mechanical, electrical and hydraulic equipment for the bridge. Our commissioning team supported installation and trained on-site operatives to use its control system.
The bridge is operated by 2 x hydraulic cylinders mounted within a concrete pit below the bridge which extend, to elevate the deck to 64°.
The mechanical equipment supply included the pivot shafts / bearings, 2 x nose locking bolts, nose end bridge support bearings and nose end shock absorbers.
The hydraulic supply included the HPU located below the bridge, operating cylinders, manifolds and pipework.
The electrical supply included the control panels including PLC kit, operators panel, switches, encoders, traffic lights, wigwags, barriers, navigation lights and cabling.
The electric panels and HPU are located within a dedicated plantroom located below the bridge. The vehicular traffic lights and barriers mounted either side of the bridge are fitted within architectural stainless steel totems which also house the operators panel.
The bridge was fabricated from S355 grade steel and after welding, was machined to allow fitting of the mechanical equipment including the pivot shafts, nose bearings and nose locks. Once complete, the structure was painted with a coating suitable for a marine environment and all of the mechanical equipment fitted, before delivery to site.
The structure was delivered to site by barge, supported on SPMT’s, so that the complete bridge could be jacked up and rotated through 90°. Once in the correct orientation the structure was then lowered on the jacks until supported on the nose end bearings and rear pivot bearings, at this stage the barge was then free to leave the site. Both edges of the bridge were fitted with bespoke stainless steel handrails and Armco crash barriers either side of the roadway.
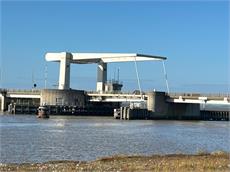
Breydon Bridge, Dutch-Style Drawbridge over the River Yare
In 2023, Qualter Hall collaborated with contractor Graham on the £7.5m upgrade of Breydon Bridge on behalf of National Highways.
Our team replaced several key components including the operating system which powers the bridge to open and close.
At the time, Ajith Nair, National Highways Project Manager said: “Many of the key components on the bridge were installed when it first opened in 1985 and are now at the end of their working life.”
What work was done by Qualter Hall on Breydon Bridge?
Replacement of hydraulic cylinders and refurbishment of hydraulic system: Drainage, removal and replacement of cylinders complete with control manifolds, major refurbishment of existing hydraulic system and replacement of pipework including flushing, pressure testing and commissioning of the hydraulic control system. This was done via a temporary scaffold system which was constructed underneath the bridge to minimise road closures.
Electrical and controls works: Design and installation of new Motor Control Center (MCC) pump starters, Programmable Logic Controller (PLC), Human-Machine Interface (HMI) and Supervisory Control and Data Acquisition (SCADA). These systems work together to control the movement of the bridge. New remote panels and cabling were also configured and installed by our team.
Commissioning and maintenance: Following installation, our Site Services team conducted Site Acceptance Testing (SAT) and delivered operator training. Quarterly maintenance visits have been made to the bridge since start-up, ensuring that it remains in optimum working condition.
About Breydon Bridge
Breydon Bridge was originally built in 1985; it is a single-span Dutch-style drawbridge with an opening span width of 23m to let boats pass underneath, along the River Yare, close to Breydon Water. The bridge carries an average of 31,000 vehicles daily on the A47 towards Lowestoft and Ipswich.